An interview with Alex Animashaun of the Tuck Bike
A few months ago, Alex Animashaun presented his prototyping process at a show and tell we held for Members of Scope of Work. Alex is a British engineer and an inventor, and his story - he’s literally reinventing the design of a bicycle wheel - was an energizing and at times eye-popping romp through exactly the topic areas that Scope of Work thrives on. Alex has been quite open about his journey on the Members’ Slack, and we wanted to give the rest of you a taste of it. So without further ado, here’s a condensed version of a chat we had with him a couple of weeks ago, before he launched a Kickstarter, about the prototypes he’s iterated through over the years.
What do you do?
I’m an engineer and each job has just taken me one little step closer to what I want to do, which is inventing stuff, creating stuff, and designing stuff. These days, I'm finally a solo inventor and I’ve been slowly and painfully bringing an idea to market for four years. Generally, bikes can only fold as small as their wheels - the wheel is indivisible. I don't want to ride bikes that have small wheels. I thought, "Well, what if you could fold the wheel?" That's the thing that my invention, Tuck Bike, does that no other bike does. You get a full-sized bike with a full-sized wheel and because the wheels fold it collapses to a smaller package.
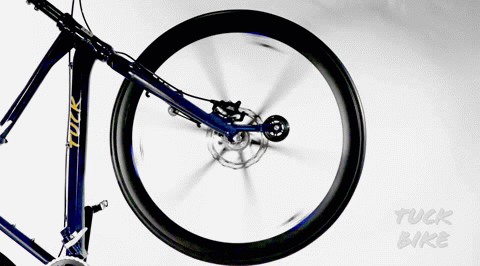
Basically, I'm self-funded. I do some freelance work on the side as a mechanical engineer. For most of my career, I've worked in automotive so it's handy to be able to get Bay Area freelance engineering rates to keep my head above water. I have to be real about it: my wife has a really great job with a tech money salary and if it wasn't for that, I could not pursue this. Sometimes you get stories of the bootstrapped inventor who did this or did that, and you're like, "Damn, how did they manage to do that?" So I want to scene-set on that - I earned some money before doing this.
How did you get here?
I studied sports engineering, and I’ve spent the rest of my life explaining what sports engineering is. It’s basically mechanical engineering. If you're a civil engineer, you learn about stresses and strains and you look at bridges. We were looking at tennis rackets or bicycles; our examples were in sport.
The first job I did out of university, I ended up getting this job as a manufacturing consultant and went around factories speeding stuff up and I hated it. I was like, "Oh no, this is terrible." The rest of my career has been just a massive course correct, with each job taking me one little step closer to what I want to do, which is invent stuff. I was at Jaguar Land Rover for a few years, which holds a very warm place in my heart, but at such a big company it was very hard to find where the actual engineering was happening. A huge amount of the work is managing suppliers, while the supplier does the engineering.
I ended up getting this job at a car start-up in Kenya. I was working as their senior test engineer, in charge of designing a car from scratch. In Kenya, pretty much all cars are imported second-hand and you have to pay a 100% import duty. So to import a $10,000 second-hand car, it becomes $20,000. It's like "Hmm, there's a business opportunity here. Can we make a brand new car for that?” But if you look at the business model in black and white, you're like, "Right, you are trying to start a car company, have you got loads and loads of money? No. Are you in an area where you can just get loads of automotive engineers and suppliers? No actually, the exact opposite of that." Yeah. Pretty hard that. It's a hard, hard thing to do.
How did you start building bike wheels?
Sometimes you go away, you come back, you see things afresh. I had gone back to visit the UK and saw the Brompton bikes with their small wheels whizzing around, and I was like, "Oh, I just don't want to ride those. They just don't look cool." And then I started thinking, "Is there another way to do it? Right, maybe you can fold the wheel." I started working on them in Kenya, coming up with stuff in my spare time. I was like, "Oh! Maybe the wheel can just fold into three pieces." If you just fold it in half, you still have the longest dimension of a wheel, the diameter. So you need to fold it in thirds for the radius. I got some welders from work, and I basically got them to moonlight evenings and weekends. Very quickly, I had a rideable folding wheel that worked. It was so basic and the wheel weighed an absolute ton, it was made of square steel tubing.
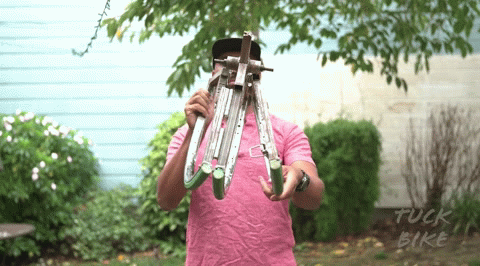
It’s a huge challenge trying to prototype hardware in developing economies. I couldn't buy aluminum, and I certainly could not have bought carbon fiber. The one place where I could buy aluminum, told me, "Oh, we’re sort out of stock." Once a year they would get a container from China, and they were out. They're like, "You know, this aluminum, this is a new technology, it's only just starting to come in here in Kenya." I was like, "New technology? It's an element!” People are just making stuff out of steel there.
Getting a true wheel is just essential. I tried loads of different ideas for how to fold the wheel and how to support the structure. I used the makerspace Gearbox to make some of my early prototypes. The hinged wheels were pretty straight, considering they were made without fixtures, but the spokes were at the end of the spans, 120 degrees apart. As you rode, you could feel some compliance, then complete rigidity with each rotation of the wheel.
I learned the hard way how the wheels work. The tensioned spoke wheel is just genius. It's a structure that's completely air - it's a masterpiece. To really understand it, I had to improve my fundamental mechanical physics, which is humbling to do as an engineer. That's something I like about [Scope of Work]: in some organizations or communities I've been in, you can't admit that you need a refresher on some fundamental thing, and [Scope of Work]'s a cool place that you can be like, "Don't tell anyone I'm asking this, but how does this work again? Does anyone know?"
Anyway, with a wire-spoked wheel, all the spokes are in tension. When you put it on the ground and apply some load, you are pushing down through the hub and the bottom of the rim flattens slightly, and because it flattens, the distance between the ground and the hub decreases, reducing tension in the bottom spokes. And the rest of the rim pushes outwards, increasing the distance to the hub and thus the tension in the other spokes. That is how the wheel distributes the radial load.
What did the refinement process look like?
My wife and I then moved to America, and I joined the makerspace formerly known as TechShop to continue prototyping and had another welder help me. The folding wheels that had hinges, folding out of plane like a book, were quick to fold, but I didn't think this was the right way to load a hinge and I doubted whether I'd be able to make the wheels true. I started building wheels that fold by lifting one piece, twisting it around, and stacking it on the other. Imagine you have a pizza in front of you, cut in three slices. Do that again and you have three slices stacked together.
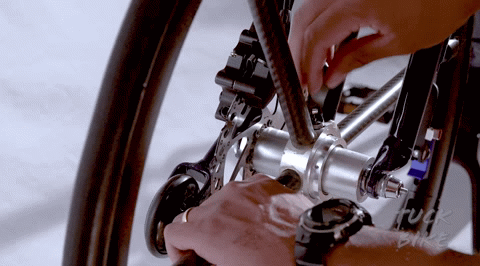
The wheel is locked at each rim joint and the hub. The rim joints have a clamp that you slide in and out of place and then tighten, and the hub has a simple clamp. The clamps mean that the whole wheel is made whole, with no play at any joint, and they’re now built with fixtures during the bonding process, meaning we get a straight wheel every time.
In the first wheels, there were 120 degrees between spokes and a large unsupported span, with a shallow section rim. That meant you could feel a difference in wheel stiffness as it rotated. Using six spokes, 60 degrees separation, and deep rims spreads the load and fixes the wheel deflection. If you ride it now, you'd have no idea it was a folding wheel.
I worked through tons of prototypes, loads of designs. You just fail, you pick yourself back up. I learned about galling, basically forming cold welds. I had an aluminum collar rotating on an aluminum hub, it would gall and just become cold-welded. I was like, "Another problem to solve." But, through perseverance, or good fortune, I'd managed to solve the problems. There's somehow a different mindset of when you've got a salary and this is your job and someone has said, "This is possible." The whole way through, I didn't know if it was possible. With the testing, I would get a little bit closer, a little bit closer, a little bit closer.
I built a test rig in my backyard because it was costing me $600 to ship a wheel to Belgium, and then like $350 or $400 to test it there. I was like, I can't afford that, so I built this drum that rotates. The drum spins at 25 kilometers per hour, and there are these bumps stipulated in the ISO standard. The wheel has to support 640 newtons of load. The drum spins and then you count all the bumps and it has to do three-quarters of a million impacts. It’s pretty brutal, the test. The wheel has to survive.
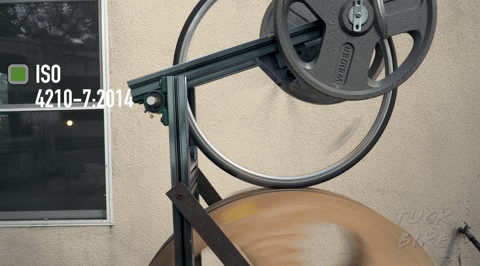
Eventually, I reached a point where I was like, "Okay, this can be done." I got help finding a bike manufacturer, and pre-pandemic, I visited Taiwan and China. The pandemic has really impacted me terribly. The bike boom means that everybody's buying bikes, and there's just no spare capacity. No one wanted to take on a tiny minimum order quantity from me. But fortunately, I've got a sample of the bike that is on its way from my contract manufacturer in China. It's my design, they've welded the bike, they've painted it, my wheels are in it.
What's next?
When I moved to America, I had six months of job hunting. I've had periods of job hunting before, I know that I am pleasant to work with, and I know I'm smart. I'm not a genius, but I'm smart, and I've got Jaguar Land Rover on my resume. But it was super hard for me to get a job, and there was definitely racism in my job interview processes. Just weird stuff, aggressive interviews. I'm like, "I'm a very pleasant person and I'm charming in an interview, especially. What's this aggression about? This is very rude.”
I was just furious at how I'd been treated in interviews. It was kind of like a, "Fuck you, I don't need your job, I'm gonna create my own thing." That's also part of why I haven't taken any investment money - I want to be captain of my ship and not be beholden to other people. But launching the Kickstarter is going to be live or die for the company. This is another thing about privilege - I’ve had tons of head starts and hands up in life, and still, I'm experiencing this stuff. Because my wife earns good money, I've been able to be like, "Right, fuck you, I'm doing it." Most other people do not have the opportunity or the resources, they just have to suck it up and play the game.
With Tuck bike, it's not a branding exercise, it's like: "No, this is me.” I'm doing something that other brands can't do. I'm folding the wheel, it's heresy! Senior people at bike companies have told me that straight. I run my own ship and that means I get to have fun with it. If that's dressing up as Dracula and jumping out of a coffin with a folded bike, so be it. This isn't bragging, but I'm a funny guy and that comes out in my branding. Also, it can't be ignored: I'm Black. In many places I've worked I had to code switch to survive. With my own business and the recent events, I can just be myself. There seems to be an assumption in branding that innovation and hard engineering have to be done by very serious people with furrowed brows and frowns, the stiffer the better. Nahhh!
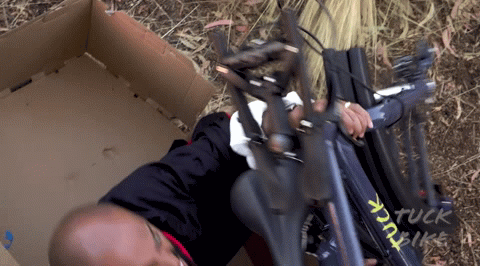
So, it's been a super emotionally and mentally challenging thing. It hasn’t been challenging physically, apart from staying up late to speak to China, and waking up early to speak to China. I've had to grow to learn marketing, import-export, working with different suppliers, the bicycle industry, accounting, freight, all of that stuff. But it's a really rewarding, fulfilling thing that I've done and if it comes to nothing, then I'll still be glad I did it.
Thanks to Alex for sharing his process, and to all the Members of Scope of Work who have been part of the ongoing conversation about wheel development on Slack!